Petek, 21. 2. 2025, 22.39
1 mesec
Obisk tovarne BMW Landshut pri Münchnu
Ozadje tovarne BMW: slovensko ime na motorju, roboti pa že v lasti Kitajcev #foto
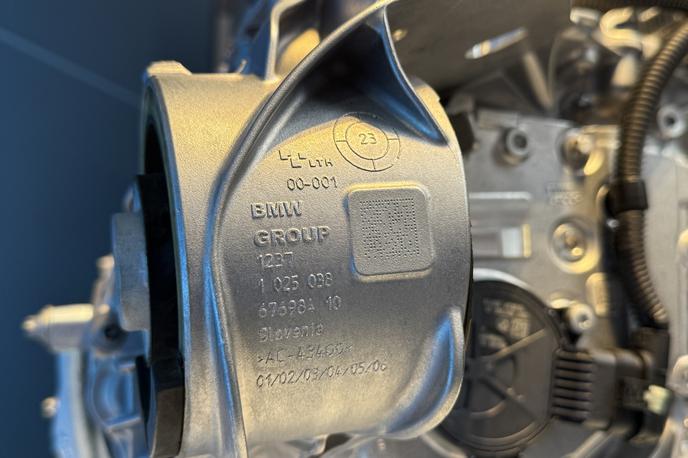
Ohišje elektromotorja, ki ima tudi oznako LTH Castings in napis Slovenia.
Bistvo razvoja in proizvodnje BMW vsaj v Nemčiji niso več motorji, temveč novodobni možgani avtomobilov. Opazni so slovenski dobavitelji, nemški roboti v vse bolj avtomatizirani proizvodnji pa so že v lasti Kitajcev. Ozadje tovarne Landshut pokaže tudi, kako je izdelava avtomobilov neue klasse razpeta med Nemčijo, Avstrijo in tudi Madžarsko.
Tovarna BMW v mestu Landshut ima 4.700 zaposlenih.
Po gneči na južni in vzhodni obvoznici okrog Münchna proti jugovzhodu vodi nekaj kilometrov značilnega nemškega Autobahna. To so lahko kilometri brez omejitve hitrosti, kjer pa so ta dan le redki vozili kaj bistveno hitreje kot 130 kilometrov na uro. Avtocesta je pripeljala do mesta Landshut, največjega mesta v Spodnji Bavarski in na splošno enega najbogatejših mest na Bavarskem.
Landshut je močno industrializirano mesto, kjer je na prostranih zemljiščih že konec šestdesetih let svojo tovarno postavil tudi BMW. Bavarski avtomobilski mogotec danes v tej tovarni izdeluje mnoge pomembne sestavne dele svojih avtomobilov in tako bo tudi v prihodnje, ko BMW na tehnologijah neue klasse načrtuje svoj projekt stoletja. Pogled v zakulisje tovarne in tudi načrtov uprave v Münchnu je razkril mnoge zanimivosti in odprl več pomembnih vprašanj, s katerimi se ukvarjata nemška in evropska avtomobilska industrija.
Joachim Post, ki je kot član uprave BMW zadolžen za dogovore z dobavitelji in dobavo delov.
BMW tradicionalnih motorjev ne izdeluje več v Nemčiji
Skoraj 60 let od vzpostavitve tovarne se je okrog Landshuta spremenilo marsikaj. Po Autobahnu se večina vozi pod klasično avtocestno omejitvijo hitrosti, pri znamki BMW (Bayerische Motoren Werke) pa proizvodnja motorjev ni več v pravem središču pozornosti kot nekoč.
BMW svojih klasičnih motorjev z notranjim izgorevanjem namreč ne izdeluje več v Nemčiji, so pa doma pustili razvoj elektrosistemov in novih generacij svojih električnih avtomobilov. Tu je zdaj razvoj najbolj pomemben in skokovit, medtem ko so pri klasičnih pogonih napredki le še malenkostni. To je bila tudi rdeča nit pogovorov med obiskom tovarne, kjer je BMW razkril nove podrobnosti tehnologij pod oznako neue klasse.
"Stavimo na modularnost pogonov in ponudili bomo široko izbiro. Zavezani smo zmanjševanju ogljičnega odtisa in od tega ne odstopamo. Električni pogoni bodo v porastu, toda ta prehod ne bo povsem linearen. Do leta 2030 želimo naš delež električnih vozil povečevati do okrog 50 odstotkov," je v Landshutu povedal dr. Joachim Post, ki je kot član uprave BMW zadolžen za dogovore z dobavitelji.
Pogled na baterijo šeste generacije in nadzorno enoto, ki je srce novodobnega električnega avtomobila z 800-voltne platforme.
Pogled na peto generacijo (desno) in šesto generacijo baterije.
Bolj kot motor pomembni postajajo možgani avtomobila
Namesto razvoja novega bencinskega (ali dizelskega) motorja je zdaj pomembneje imeti dovolj znanja, da proizvajalec izdela kar najboljše možgane avtomobile.
To je enota za nadzor in upravljanje baterije (battery management system), ki upravlja vse kompleksne operacije, nadzoruje toploto, skrbi za učinkovito polnjenje in kar najboljši izkoristek energije.
To znanje je bilo med razlogi, da sta v hrvaški Rimac denar vložila tako Porsche kot Hyundai, pri BMW pa so možgane za prihodnost razvili samostojno. Zato ni bilo presenetljivo, da so tudi v Landshutu ta sistem – poimenovali so ga energy master – tako zelo izpostavili.
Pogled na baterijo v peti in novi šesti generaciji BMW-jevega električnega pogona hitro pokaže na precejšnje razlike, o katerih smo pisali že včeraj.
Elektromotorji so vse bolj kompaktni in lahki, kar omogoča boljši prostorski izkoristek avtomobilov.
Elektromotor je tako majhen, da bi ga kar prijel v roko in odnesel na drugo stran sobe
Elektromotorji so izjemno majhni. Zdi se, kot da bi lahko sprednjega kar prijeli v roke in ga odnesli na drugo stran sobe. Tak motor ima maso le nekaj več kot 70 kilogramov, a vseeno moč od 120 do 180 kilovatov. Zadnji motor je še nekoliko zmogljivejši in tudi večji, zato tudi masa znaša že okrog 120 kilogramov.
Oba motorja skupaj predstavljata manj kot deset odstotkov skupne mase avtomobila, in ker so kompaktni, jih bodo lahko v avtomobile vgradili tudi po tri ali štiri naenkrat.
Nov del tovarne za proizvodnjo enote za baterijski in toplotni nadzor avtomobila. Izstopajo oranžni roboti nemške znamke Kuka, ki pa je od leta 2016 v večinski kitajski lasti.
Vsi električni avtomobili pri BMW bodo imeli motor na zadnji osi, ki je osnova pogona.
Slovensko ime na aluminijastem ohišju
Na zadnjem delu ohišja zadnjega motorja smo opazili tudi napis Slovenia, saj gre za del, ki ga za BMW dobavlja slovensko podjetje LTH Castings. To je podjetje iz Škofje Loke, ki je specializirano za visokokakovostne komponente iz tlačno litega aluminija.
Tako kot bencinskih in dizelskih tudi elektromotorjev za neue klasse ne bodo izdelovali Nemci, temveč Avstrijci. V tovarno Steyr, ki ima že 40-letno tradicijo, so vložili milijardo evrov in jo prilagodili novim potrebam. Tam bo do leta 2030 predvidoma polovica od 4.700 zaposlenih delala na področju rešitev za električna vozila.
BMW ima v Steyerju svojo največjo tovarno za motorje. Tam lahko letno izdelajo 600 tisoč elektromotorjev, še naprej pa bodo izdelovali tudi bencinske in dizelske motorje.
Vodja tovarne v Landshutu, v ozadju pa koncept električnega SUV neue klasse.
Pomen vertikalno usmerjene proizvodnje, BMW vlaga tudi v izdelavo aluminijastih odlitkov
Elektromotorje so začeli proizvajati šele pred kratkim. Vgradijo jih v aluminijasto ohišje, ki ga BMW v Landshutu ulije samostojno, in sicer prek napredne tehnologije visokotlačnega ulivanja. Da BMW vlaga dodatna sredstva v lastno proizvodnjo aluminijastih elementov, je poleg lastnega razvoja praktično celotnega baterijskega pogona šeste generacije zelo jasen primer težnje po znatnejši vertikalni proizvodnji.
Pri tej proizvajalci več sestavnih delov izdelajo sami in so manj odvisni od zunanjih dobaviteljev. Tak pristop so že utemeljili Tesla in Kitajci, med zadnjimi predvsem BYD. Kaj bo to pomenilo za obseg prihodnjih poslov za zunanje dobavitelje?
Prvi predserijski primerki avtomobila neue klasse iz tovarne v madžarskem Debrecenu.
Avtomobile bodo najprej izdelovali Madžari, kaj torej ostane Nemcem?
Ko v Landshutu pripravijo ohišje motorja in vanj Avstrijci vgradijo potrebno tehnologijo, motorje pošljejo na Madžarsko. Tam bodo letos poleti začeli serijsko proizvodnjo prvih avtomobilov generacije neue klasse, predserijske avtomobile pa so Madžari že izdelali.
Kaj torej ostane Nemcem? BMW je pilotne tovarne za visokonapetostne baterije postavil v Parsdorfu, Hallbergmoosu in Münchnu. Strokovno podporo so prav tako zbrali v Münchnu. V tovarni Landshute načrtujejo širitev za lastno proizvodnjo omenjenega sistema energy master – ta je torej eden najpomembnejših delov novih, še posebej električnih avtomobilov. Pri šesti generaciji je to sploh prvič, da je BMW ta del avtomobila razvil samostojno.
Za isto mizo delata človek in robot
Proizvodnja tega sistema je že močno avtomatizirana, na posameznih postajah v proizvodnji za isto mizo delata tako zaposleni kot njegov sodelavec robot. Ti so odlični za visokofrekvenčna ponovitvena dela, kjer bi človek slej ko prej naredil napako, medtem pa imajo roboti še določene težave tam, kjer je potrebnega nekaj več človeškega občutka ob prijemu. V energy master na primer robot težje prime, upogne in optimalno vstavi visokonapetnostni kabel kot zaposleni z dolgoletnimi izkušnjami.
Oznaka neue klasse ni namenjena le električnim vozilom, saj označuje skupek tehnoloških novosti za avtomobile vseh tipov pogonov.
Oranžni roboti so nemški, a že v kitajski lasti
Še ta zanimivost: BMW bo imel v Landshutu ob koncu širitve že prihodnje leto okrog 400 robotov, ki so večinoma vsi kričeče oranžne barve. To so roboti priznanega proizvajalca Kuka. Gre za nemško podjetje, ki so ga ustanovili že pred 127 leti in v zadnjih desetletjih velja za enega vodilnih dobaviteljev inteligentnih avtomatiziranih proizvodnih procesov.
Tudi to podjetje iz Augsburga pa so leta 2016 večinsko že prevzeli Kitajci – natančneje Midea Group, ki je takrat za prevzem odštela 4,5 milijarde evrov.
Surovine za baterije dobavljajo Kitajci, a kako dolgo še?
Kitajci so za zdaj seveda nepogrešljivi pri dobavi celic za baterije. Med dobavitelji je tudi CATL, največji proizvajalec baterij na svetu.
Tako bo ostalo še nekaj časa, saj imajo Kitajci večino surovin za baterije. BMW veliko stavi na reciklažo baterij in to ne le iz ekoloških vidikov – pomemben je tudi strateški položaj manjše odvisnosti od dobaviteljev iz Azije. Na daljši rok bo tudi dobava surovin postala del vertikalno usmerjene proizvodnje avtomobilov, ki za proizvajalca, kot je BMW, prinaša stabilnost in večjo stroškovno konkurenčnost.
Iz reciklaže pridobljeni litij, nikelj in kobalt so skoraj stoodstotno primerljivi s surovino naravnega izvora. A proces reciklaže baterij se ni še niti začel; baterije v večini električnih avtomobilov so še nove, še pred reciklažo jih bodo marsikje uporabili v drugotne namene – najočitneje za hranilnike, ki v energijskem ekosistemu postajajo vsem pomembnejši.
Joachim Post: Nihče nima kristalne krogle
Na temo razvoja avtomobilov s klasičnimi motorji tokrat v Landshutu niso povedali veliko. Dejstvo je, da se klasični pogoni pri BMW prav kmalu še ne umikajo in da danes kljub dejstvu, da so Bavarci med premijskimi znamkami pri preboju elektromobilnosti najuspešnejši, električni avtomobili predstavljajo manj kot petinski delež celotne prodaje. Po oceni Posta bi se lahko delež električnih vozil do leta 2030 pri BMW dvignil do 50 odstotkov. Če se bo to res zgodilo, bo v tem obdobju znatneje padla prodaja klasičnim avtomobilom.
"To je naša ocena, žal pa nihče med nami nima kristalne krogle. Marsikaj se lahko zgodi, zato smo tudi pripravljeni na različne tehnologije. Naše baterije lahko sprejmejo tudi celice tipa LFP," je povedal Post. Glede tako imenovanih solid state baterij pa je bil Nemec jasen: za zdaj o njih resneje ne razmišljajo in tako bo še več let. Glede na novo 800-voltno platformo bodo namreč potrebni časi za polnjenje novih električnih BMW-jev tako kratki, da potrebno doplačilo za nov tip baterij z večjim dosegom tudi za končnega kupca še ne bi imel pravega smisla.